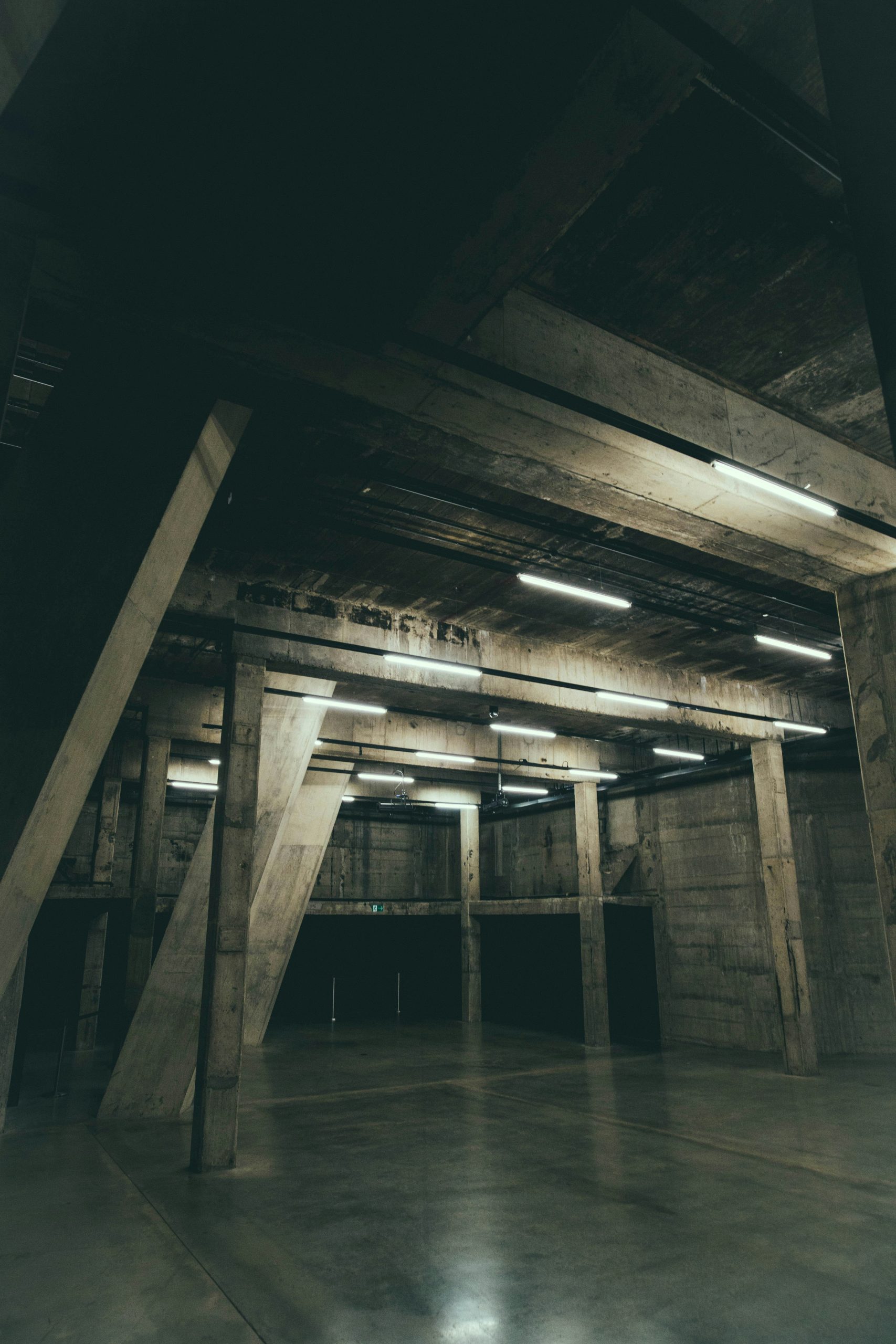
How High Temperature Sealant for Industrial Use Improves Performance
Agnes
- 0
Introduction to High Temperature Sealant for Industrial Use
In the fast-paced world of industrial operations, efficiency and reliability are paramount. One often overlooked hero in this quest for peak performance is the high temperature sealant. These specialized materials aren’t just another addition to your toolbox; they serve as critical components that enhance durability and decrease downtime. Whether you’re working with machinery exposed to extreme heat or sealing joints that endure intense stress, the right high temperature sealant can make all the difference. Discover how this essential product elevates industrial applications and why selecting the right one matters more than ever. Let’s dive into the fascinating world of high temperature sealants for industrial use!
The Importance of Choosing the Right Sealant
Choosing the right sealant is crucial for ensuring longevity and performance in industrial applications. A mismatch can lead to costly failures, downtime, or even safety hazards.
Different environments present unique challenges. Factors like temperature fluctuations, chemical exposure, and mechanical stress must be considered when selecting a sealant. High temperature high temperature sealant sealants are specifically formulated to withstand extreme conditions without degrading.
Furthermore, using an inappropriate sealant may compromise the integrity of machinery or components. This not only affects operational efficiency but can also impact product quality.
Investing time in choosing the right high temperature sealant pays off significantly. It ensures reliable performance over time and minimizes maintenance costs down the line. Remember that proper selection directly correlates with overall productivity and safety in any industrial setting.
Advantages of Using High Temperature Sealant in Industrial Settings
High temperature sealants are essential in industrial environments where extreme conditions prevail. They withstand elevated temperatures, ensuring that machinery and equipment remain protected even under intense heat.
One significant advantage is their durability. These sealants resist degradation from thermal cycling, maintaining integrity over time. This reliability leads to fewer maintenance interruptions.
Additionally, high temperature sealants offer excellent adhesion properties. They bond effectively to various materials like metals and composites, creating a robust barrier against leaks and contamination.
Furthermore, they provide resistance against chemicals and solvents commonly found in industrial settings. This capability safeguards components from potential damage caused by harsh substances.
Using high temperature sealants can lead to increased efficiency. By preventing leaks or failures, businesses can minimize downtime and enhance overall productivity within operations.
Common Applications and Uses of High Temperature Sealant
High temperature sealants are crucial in various industrial applications where heat resistance is vital. They find extensive use in automotive manufacturing, particularly around exhaust systems and engine components. These areas experience extreme temperatures that can compromise standard materials.
In the aerospace industry, high temperature sealants are essential for sealing joints and gaps in engines and fuel systems. Their ability to withstand harsh conditions ensures safety and performance during flight operations.
Manufacturing plants also rely on these sealants within machinery that operates at elevated temperatures. Equipment used in chemical processing or oil refining requires robust sealing solutions to prevent leaks and enhance durability.
Additionally, high temperature sealants support construction projects involving fireplaces, boilers, or kilns. They provide a reliable barrier against heat transfer while maintaining structural integrity over time. This versatility makes them an indispensable part of many industries striving for efficiency and safety.
Factors to Consider When Selecting a High Temperature Sealant
When selecting a high temperature sealant, consider its temperature resistance. Not all sealants can withstand extreme heat levels. Knowing the specific temperatures of your application is crucial.
Next, evaluate the chemical compatibility of the sealant with any substances it may encounter. This ensures durability and prevents breakdown over time.
Flexibility is another important factor. A good high temperature sealant should be able to accommodate movement without cracking or losing adhesion.
Look into curing times as well. Some projects require quick-drying options to minimize downtime, while others might have more flexibility in this area.
Always check for manufacturer recommendations and certifications to ensure that you’re choosing a product suitable for your industrial needs.
How to Properly Apply and Maintain High Temperature Sealant
Proper application of high temperature sealant is crucial for optimal performance. Start by preparing the surfaces thoroughly. Clean them to remove dust, grease, and any previous sealants. This ensures a strong bond.
Apply the sealant evenly using a caulking gun or similar tool. Aim for consistent pressure while squeezing out the product to avoid uneven lines or gaps. If necessary, smooth it with a putty knife for an even finish.
Curing time varies based on manufacturer specifications; follow these guidelines closely. Avoid disturbing the seal until it has fully set.
Maintenance involves regular inspections, especially in high-stress environments. Look for signs of wear or degradation after significant temperature fluctuations or prolonged exposure to harsh conditions. If you notice cracks or peeling, address them promptly by removing old sealant and reapplying fresh material as needed. Keeping up with maintenance prolongs effectiveness and enhances durability.
Conclusion: Enhancing Performance and Efficiency with High Temperature Sealants
High temperature sealants are invaluable in industrial environments. They provide robust protection against the challenges posed by extreme heat and harsh conditions. By ensuring tight seals, these products not only prevent leaks but also enhance equipment longevity.
Utilizing high temperature sealants leads to improved operational efficiency. Equipment runs smoother and requires less maintenance, which saves time and costs over the long term. Industries can count on specialized formulations tailored for specific applications, ensuring that performance remains optimal even under pressure.
Choosing the right high temperature sealant is crucial for maximizing these benefits. With thoughtful selection and proper application techniques, businesses can achieve significant improvements in both performance and reliability. Investing in quality sealants pays off through enhanced productivity and reduced downtime.
Embracing high temperature sealants ultimately drives success across various industrial sectors, reflecting a commitment to excellence in operations while prioritizing safety and durability.